Riding the Curve: Leesburg Concrete’s Role in the Jupiter U.S. 1 Bridge Project
When you're building something that thousands of people will drive, bike, and walk over every single day—right over water—there’s not much room for guesswork.
That’s the kind of challenge that brought Leesburg Concrete into the fold on the Jupiter U.S. 1 Bridge replacement project, a major Florida Department of Transportation (FDOT) initiative. It’s a big deal for the community—wider lanes, bike paths, and safe pedestrian access—but what made this project stand out for us was the technical complexity of the architectural precast concrete cladding.
Why This Project Was Unique
FDOT needed architectural precast concrete cladding panels that weren’t just for looks. They had to:
- Fit a cast-in-place bridge with compound curves
- Be both radius and tapered, matching a dynamic, variable shape
- Withstand Florida’s coastal environment and meet all DOT structural and aesthetic requirements
- Be installed cleanly, quickly, and accurately on-site over water
This wasn’t your average precast concrete cladding job—it required a high level of precision from start to finish.
From the Shop to the Shore
Our team engineered and produced each piece to tight tolerances, modeling and refining the design before a single panel was poured. A lot of the work happened well before the concrete hit the forms.
Here’s what that process looked like:
- Extensive pre-production reviews to match complex bridge geometry
- Close collaboration with contractors for seamless installation
- Use of durable materials designed specifically for long-term performance in coastal conditions
- Transport and logistics planned down to the hour for just-in-time delivery to the job site
The goal was simple: deliver precast architectural concrete solutions that installed smoothly, fit perfectly, and held up to both engineering standards and environmental demands.
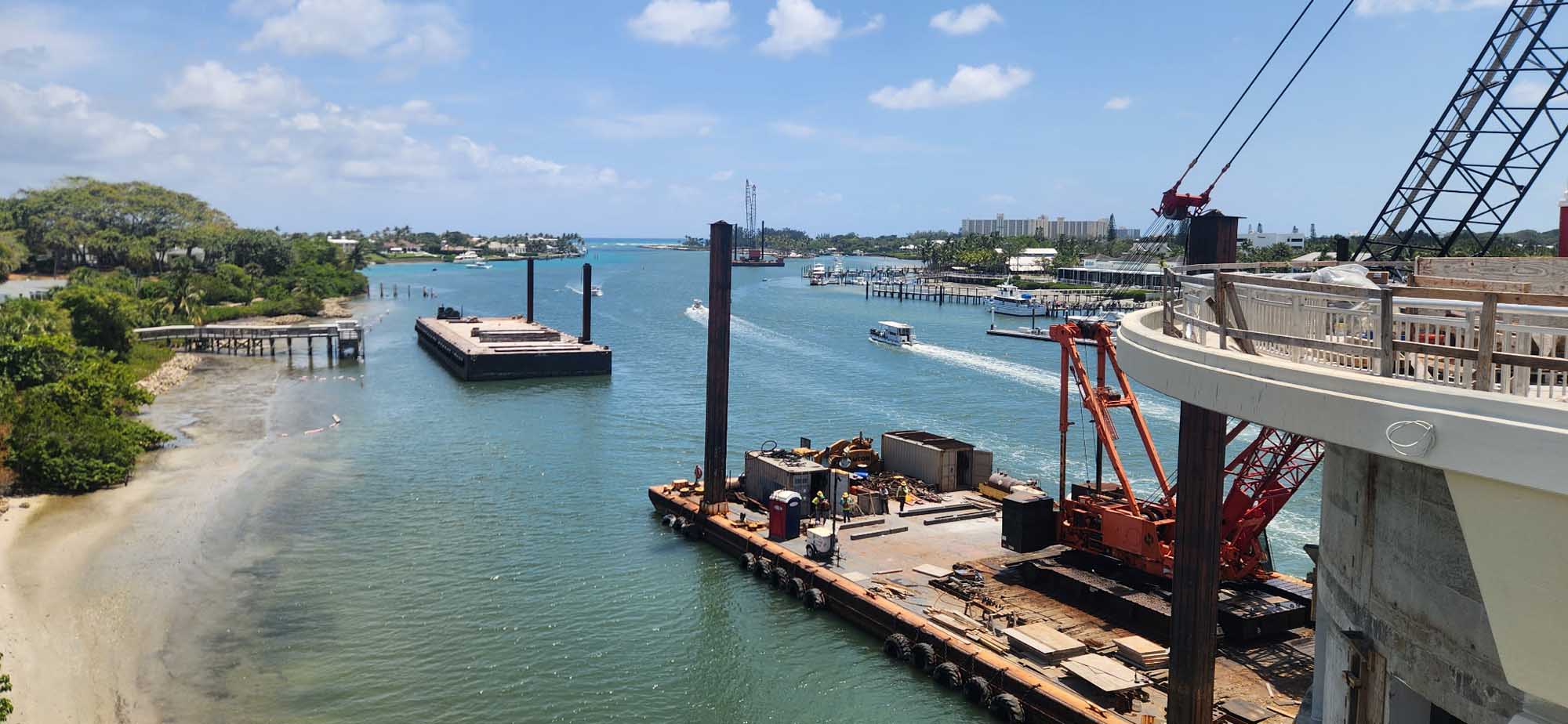
Installation in Action
You can see from the job site photos—each panel had one shot to fit exactly right. Crews worked over water, placing curved precast concrete cladding panels onto a structure that demanded precision.
When you’re installing over water, margin for error is almost nonexistent. That’s why every dimension and anchor point was verified and reverified before the first crane pick.
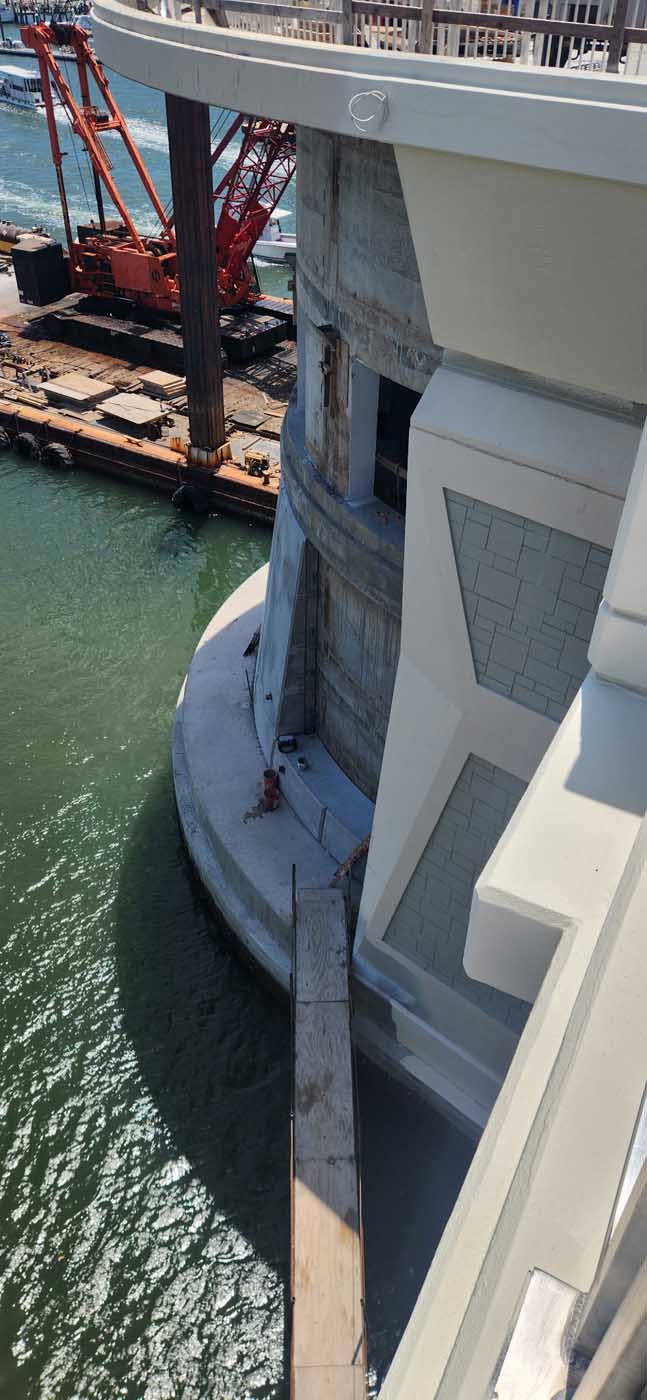
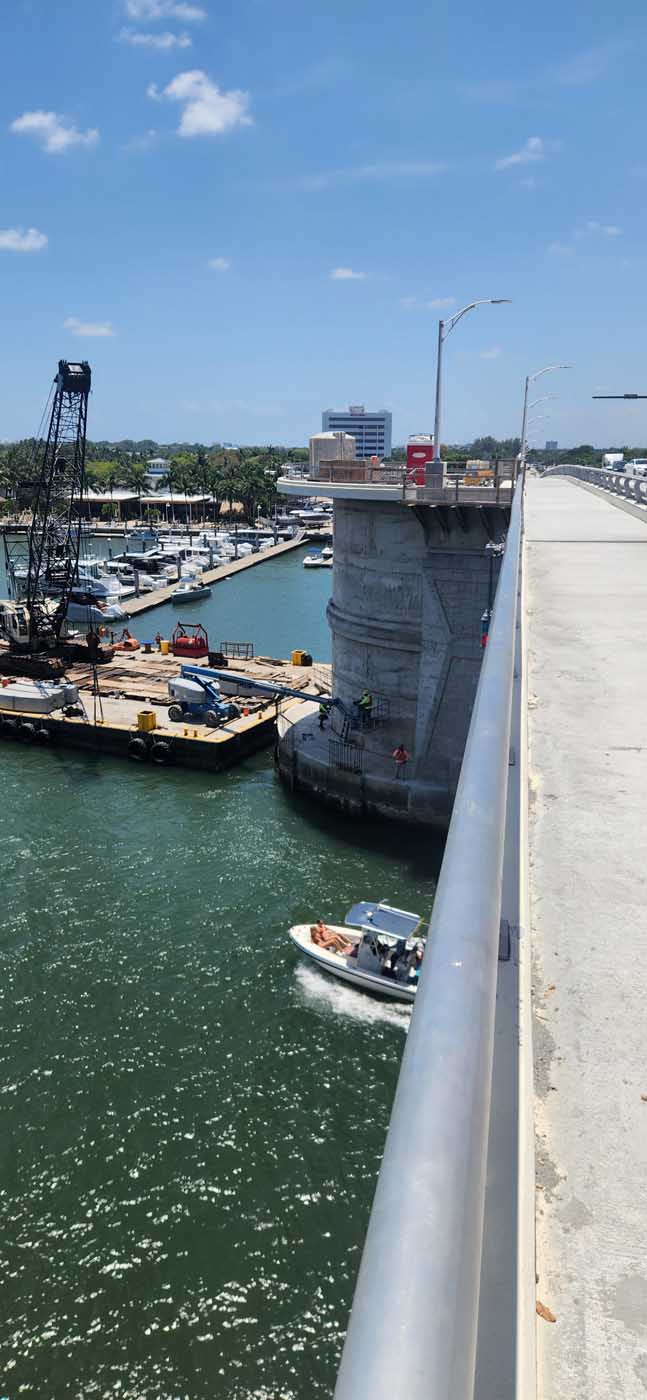
The Final Result
Today, the Jupiter U.S. 1 Bridge is open in its new configuration, offering:
- Two travel lanes in each direction
- Dedicated bike lanes
- Wide sidewalks for safe pedestrian access
And wrapped around it all is a custom precast concrete panel cladding system—built to match the curves of the bridge, endure the coastal environment, and maintain a clean architectural finish for decades to come.
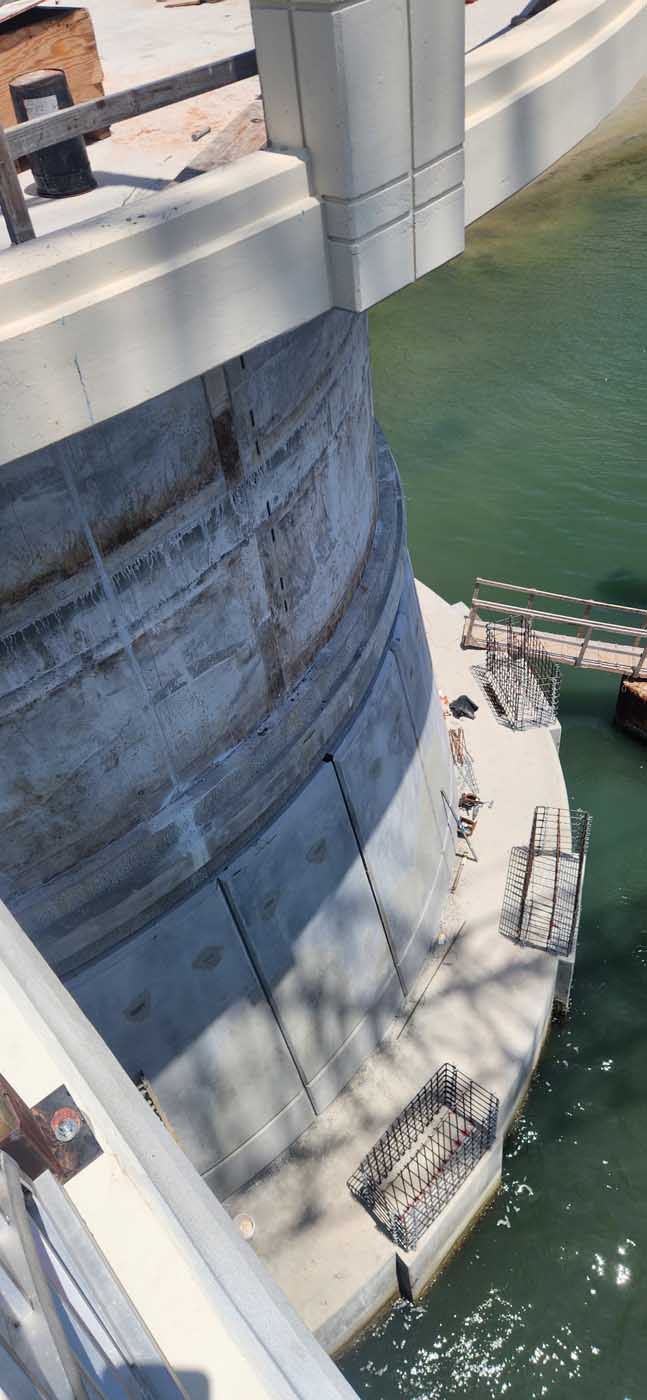
A Quick Note to Our Industry Partners
If you’re a contractor, engineer, or municipal planner working on a project that demands specialty precast concrete cladding, precast concrete panel cladding, or custom architectural precast concrete work—especially when tight tolerances are critical—we’re here to help.
No pressure. Just honest experience, reliable delivery, and concrete that fits the first time. Request a quote today.